The Ultimate Guide to Properly Maintaining MHE Equipment
- Multi-Mover
- Jan 22
- 4 min read
Investing in solid MHE (Material Handling Equipment) is only half the job when it comes to trying to make material handling jobs as efficient as possible. Keeping your electric movers, tugs and other specialist equipment in top shape is what really keeps things running smoothly. Multi Mover, one of the UK’s top suppliers of electric movers and MHE gear, doesn’t just offer high-quality products - we’ve also got your back with after-sales support, including maintenance and emergency repairs. With this in mind, this guide will provide you with all of the essential info on how to keep your MHE equipment in the very best condition.
What’s the Difference Between Maintenance and Servicing?
Before we get into the fundamentals of MHE equipment maintenance, let’s quickly clear up the difference between regular maintenance and professional servicing. Both are important, but they perform different roles:
Routine Maintenance
These are the jobs your team does every day or week, like cleaning, lubing parts and performing quick checks for anything that looks off. Routine maintenance helps you catch small issues before they turn into big, expensive problems.
Professional Servicing
This is when the professionals come in. They will do a more thorough inspection into your equipment’s health, checking parts you might not even think about. Multi Mover offers tailored service packages that help keep your equipment performing at its best.
Types of Maintenance Checks
Keeping your MHE equipment in great shape means incorporating different types of checks. Here’s a breakdown of the different types of maintenance checks you can expect to complete on a routine basis:
Daily Checks
Daily checks are your first line of defense. These quick tasks help you spot problems before they snowball:
● Make sure the battery is charged and ready to go.
● Check for any obvious damage or loose bits.
● Test brakes and safety features to make sure they’re working properly.
A quick once-over at the start and end of each shift can save you from headaches later.
Weekly Maintenance
Weekly maintenance digs a little deeper:
● Give the equipment a good clean to get rid of dust and debris.
● Tighten any loose bolts or parts.
● Apply lubrication where needed.
Monthly Inspections
Monthly checks are more thorough and help catch long-term wear and tear:
● Check tire pressure and look for any signs of wear.
● Test all the control systems and buttons.
● Listen for any weird noises coming from the motor.
Make sure you log these inspections so you can keep track of what’s been done and spot any recurring issues.
Annual Servicing
Annual servicing is a must if you want your equipment to last. Multi Mover’s pros will:
● Run detailed diagnostics and performance tests.
● Replace worn-out parts.
● Calibrate everything to keep it running like new.
Signing up for an annual service plan can save you a ton of money on emergency repairs.
Why Bother with Regular Maintenance and Servicing?
Skipping maintenance might seem like an easy way to save time, but trust us: it’ll cost you in the long run. If you’re not convinced, below are just a few reasons why regular maintenance is the right option:
Keeps Things Running Smoothly
Well-maintained equipment runs better and lasts longer. Less friction means less wear, which means you won’t be shelling out for replacements anytime soon.
Keeps Everyone Safe
Faulty equipment can be dangerous, however, regular maintenance reduces the chance of accidents and keeps your team safe.
Prevents Accidents
Brakes not working? Tyres worn out? These issues can lead to serious mishaps. Staying on top of maintenance helps you avoid them.
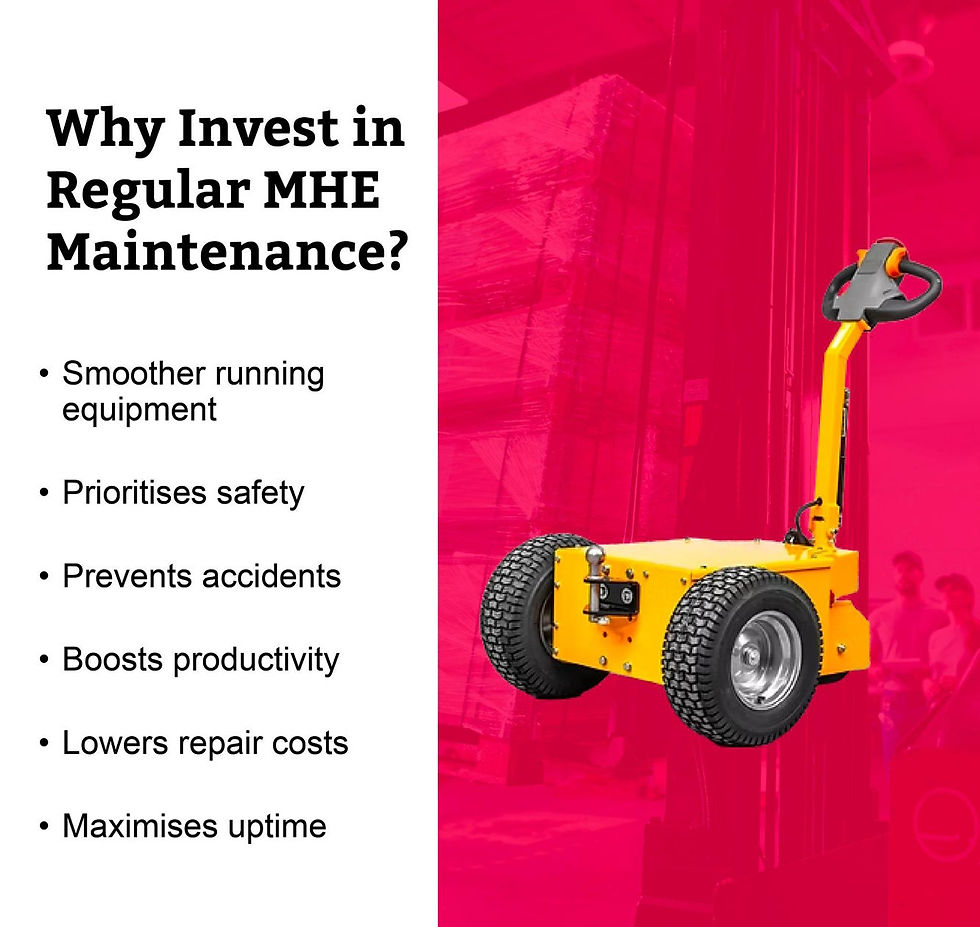
Boosts Productivity
Equipment breakdowns slow everything down. Keeping your gear in good shape means fewer interruptions and more getting stuff done.
Cuts Down Repair Costs
Catching small problems early is way cheaper than dealing with a major breakdown. Maintenance helps you avoid those big repair bills.
Maximises Uptime
You can’t afford to have your equipment sitting idle. Multi Mover’s service packages help you keep things running with minimal downtime.
Multi Mover’s After-Sales Support and Service Plans
At Multi Mover, we get it: you need your equipment to work when you need it. That’s why we offer a range of after-sales services to keep your electric movers in top condition.
Maintenance Packages
Our maintenance packages include regular check-ups and minor fixes to keep your MHE gear running smoothly. These are perfect for businesses that want to minimise downtime and get the most out of their equipment.
Emergency Repairs
Even with the best maintenance, things can go wrong. Our emergency repair service gets your equipment back up and running fast, so you don’t lose valuable time.
Custom Service Plans
Every business is different, so we offer flexible service plans that fit your specific needs. Whether you want frequent checks or just an occasional tune-up, we’ve got you covered.
Keep Your MHE Gear in Top Shape with Multi Mover
Keeping your MHE equipment well-maintained isn’t just smart, it’s also essential if you want to avoid expensive breakdowns and keep things running smoothly. With Multi Mover’s expert support, maintenance packages and emergency repair services, you’ve got everything you need to keep your electric movers in perfect condition.
Want to learn more? Head over to Multi Mover and check out our range of service plans or give us a call on 01952 771264.
Commentaires